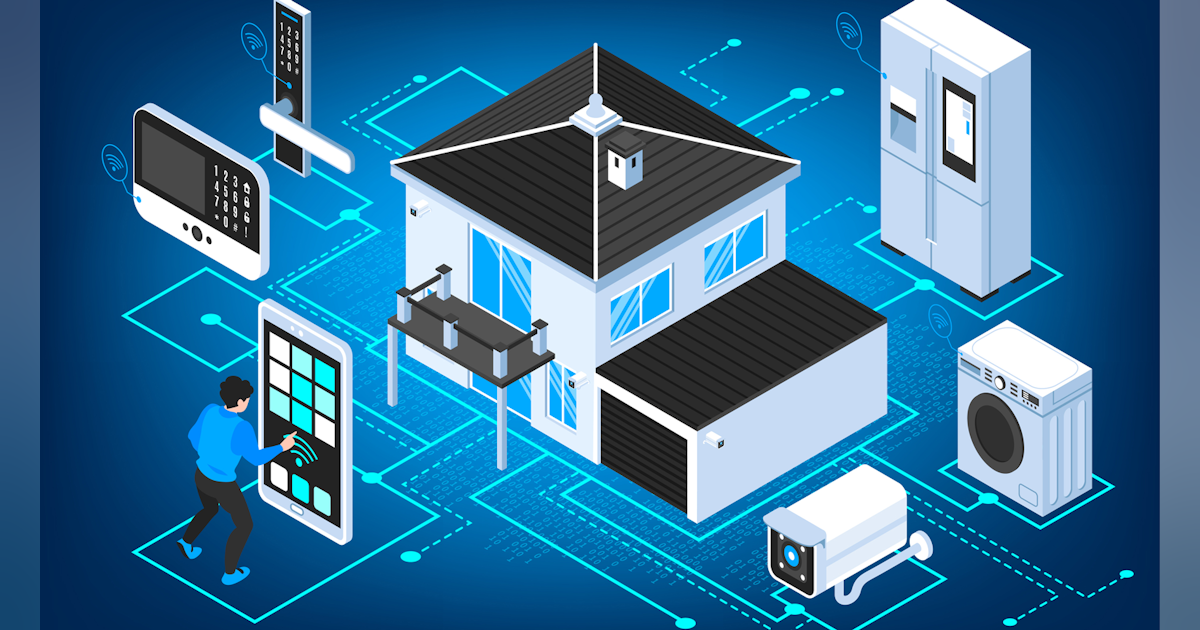
Members can download this article in PDF format.
Motors are everywhere, more than you think. If you doubt this, just try counting all of the motors in your home, car, and office that you use every day. The large motors are obvious, but it’s the small ones buried in some other object that you tend to forget. These motors are hidden and not recognizable as such, and many if not most are battery-operated.
Lots of these small motors are now showing up in office buildings, factories, and other facilities. Some home examples are the motors in smart door locks, video doorbells, video-surveillance cameras, and smart utility meters. One of the most widespread applications involves smart sanitation products, such as automatic paper-towel dispensers, faucets, soap dispensers, and smart toilets.
All of these products use small, brushed dc motors and/or a solenoid to turn things off and on after some mechanical operation. Such functions require motor-control circuits that meet design challenges like full automation, low power consumption, and small size. Some particularly challenging design needs are speed control, position detection, and stall detection. Low power consumption is essential since most of these devices are battery-operated.
Sponsored Resources:
DC Motor Drive Basics
Brushed dc motors use a commutator to continuously switch the applied voltage polarity to keep the motor rotating in one direction. Reversing the applied dc voltage polarity reverses the rotation direction. The amount of voltage applied determines the speed or rotation.
The most common way to drive a brushed motor is to connect it to an H-bridge (see figure). It consists of four MOSFET switches in the bridge arms with the motor connected across the bridge. Turning on Q1 and Q4 causes the motor to rotate in one direction. Turning on Q2 and Q3 produces rotation in the other direction. Control signals from an MCU or a separate H-bridge driver IC operate the MOSFETs.
%{[ data-embed-type="image" data-embed-id="60fecfd1a2b40c93028b48a4" data-embed-element="span" data-embed-size="640w" data-embed-alt="The classical H-bridge, consisting of two half bridges, provides the necessary motor current. It also implements an easy way to reverse motor current to reverse direction of rotation." data-embed-src="https://ift.tt/3lnPYKi" data-embed-caption="The classical H-bridge, consisting of two half bridges, provides the necessary motor current. It also implements an easy way to reverse motor current to reverse direction of rotation." ]}%
Certain dc motors use discrete MOSFETs to implement the H-bridge, but that approach consumes a considerable amount of PCB space. Today, a wide variety of H-bridge driver ICs are available to reduce PCB area and simplify motor control overall. Some of these drivers consist of two half-bridge circuits that can be connected into a full H-bridge or used separately to drive other loads such as a latching relay or solenoid.
Motor Control
To provide speed and position control, the motor driver needs feedback from the motor. This is accomplished by monitoring motor current. The motor current varies as it’s switched by the commutator, thereby producing ripples. By counting these ripples, you can determine motor speed and/or rotation position.
The motor current also can be used as a signal to stop rotation. Typically, when a brushed dc motor is first connected to dc, there’s a large inrush current. The current then decreases to a lower level during rotation. Now, if the motor stalls or its rotation is halted in some way, the current will increase sharply. That transient can be used as a ”stop” signal to the motor driver. Sensing motor current usually requires a series or shunt resistor. This may be external to the driver, although some driver ICs incorporate the sense resistor.
Integrated Protection
A beneficial feature of a motor driver is integrated protection circuits. Undervoltage lockout (UVLO), for example, shuts down the H-bridge if the supply voltage drops below a certain value. A typical value may be 1.65 V. Overcurrent protection (OCP) is another feature that detects output shorts or other instances of excessive current and provides automatic shutdown. Then there’s thermal shutdown (TSD), which cuts off power if the IC experiences a temperature beyond its stated maximum.
A “must” feature is a sleep mode that reduces current draw if the device isn’t active for a period of time.
Some of these driver features are useful in home-automation products. For example, a smart door lock uses a motor to move the deadbolt or latch for locking or unlocking. The stall detection method mentioned earlier, which involves monitoring motor current peak, can be used to turn off the motor when the lock is fully open or closed. In some cases, an external sensor may be employed to determine the end of movement, signaling fully open or closed.
Another motor use is moving an IR cut filter on a surveillance-video camera or a video doorbell. The IR filter is applied during the day, but it’s removed at night to provide sensing of the reflected IR light from objects illuminated by IR LEDs. A small, brushed motor moves the IR filter.
An example of the brushed-motor driver discussed earlier is found in Texas Instruments’ DRV82xx series. The DRV8210 packages the two half-bridges that can deliver up to 1.76 A max each with a supply voltage in the 1.65- to 11-V range. The logic supply may be 1.8, 3.3, or 5 V. UVLO, OCP, and TSD protection plus a sleep mode are included. The device comes in a 4- × 4-mm WSON package or an SOT563 1.2- × 1.6-mm package, thus taking up minimum space. Other models in this line (DRV88xx) are available, too.
Sponsored Resources:
"motors" - Google News
August 03, 2021 at 02:46AM
https://ift.tt/3A2lEsJ
Smart Control of Brushed DC Motors Improves Efficiency - Electronic Design
"motors" - Google News
https://ift.tt/2SwmEC9
https://ift.tt/3b0YXrX
Bagikan Berita Ini
0 Response to "Smart Control of Brushed DC Motors Improves Efficiency - Electronic Design"
Post a Comment